19 Aug Intelligent Imaging Innovations (3i) Collaborates With 3M to Leverage 3D Printing for Microscopy Systems
Intelligent Imaging Innovations (3i) is a Colorado-based manufacturer of microscopy devices for biomedical research including those utilizing light sheet technology for cleared tissue samples. This technology is a unique approach to light microscopy, allowing for imaging at multiple depths in a cleared biological sample. Companies around the world take advantage of 3i’s innovative technology to advance research microscopy through the entire experimental process, as the ability to image a sample at different depths represents a step-change in microscopy solutions. Due to some of the unique challenges associated with this technology, a novel and specialized sample holder is required.
3i came to 3M hoping to leverage 3D printing to manufacture sample holders meeting their low quantity production part needs at a relatively low-cost. After discussing with 3M’s design team, it was apparent to 3i that although costs were relatively similar to what they were currently paying for machined PTFE parts, the opportunity to boost the customer experience by improving functionality of the holder and print on-demand was where there was true value.
3i also utilizes three different sizes of sample holders, with the size difference between the three not obvious to the naked eye. Leveraging additive manufacturing, engraved text was printed on the holders with a sizing label on the handle to make it simpler and more intuitive.
An additional modification was made to the original connection mechanism that mates the sample holder to the microscopy device to improve support when testing. The attachment was redesigned to fit more easily and securely into a magnetic mounting mechanism, solving the support issue. 3i was able to do all of this via 3D printing without adding cost to their original design, making the business case apparent.
Finally, and potentially most importantly, 3D printed PTFE solved chemical compatibility issues with the clearing solutions required in the testing process. Before 3D printed PTFE, 3i used sample holders made from many other materials such as nylon and aluminum. These materials caused problems in testing as they could not maintain structural composure within the clearing solution, either breaking down or generated precipitates which adversely affected image quality.
“Due to a variety of tissue clearing technologies, many of which act as solvents, chemical compatibility is very important for our application,” states 3i Engineer, Ian Bloomfield. “Common plastics often lost their strength shortly after being in contact with the solvents and some common metals dissolved at the surface, causing background noise in the imaging system. PTFE solved the material problem, but traditional manufacturing methods limited the geometry capabilities, so we looked to 3M’s 3D printed PTFE. Partnering with 3M was incredibly beneficial for both us and our customers offering flexible sample mounting geometries and chemical compatibility across a variety of clearing solutions.”
Taking further advantage of 3D printing, 3i sees potential for customizing sample holders for each customer so that it fits their exact testing needs and requirements.
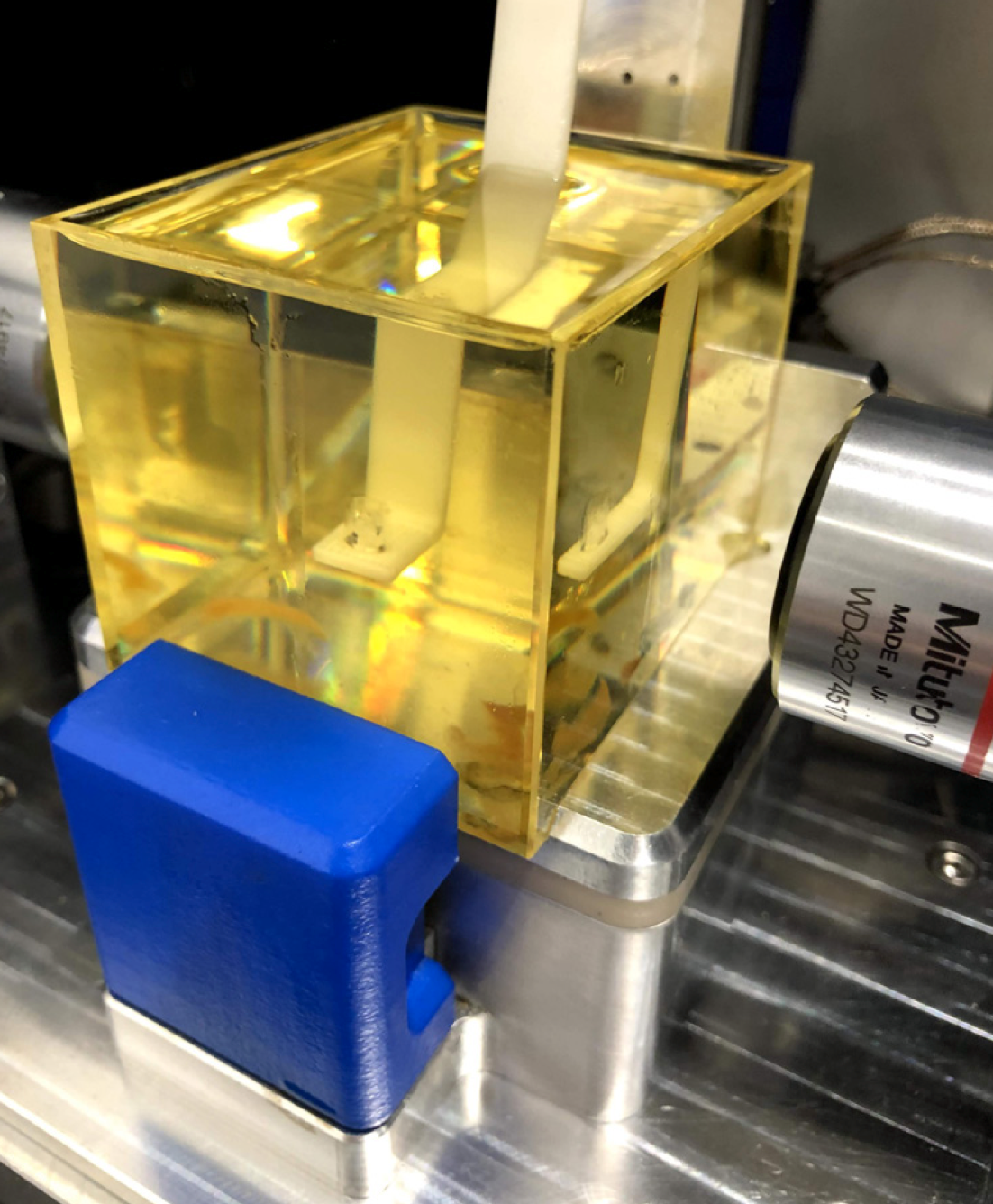
Originally posted by 3M Advanced Materials Division at the link below:
Media Contact
Sergei Sorkin
Director of Marketing, 3i
Phone: +1 303 607 9429
Email: sergei@intelligent-imaging.com